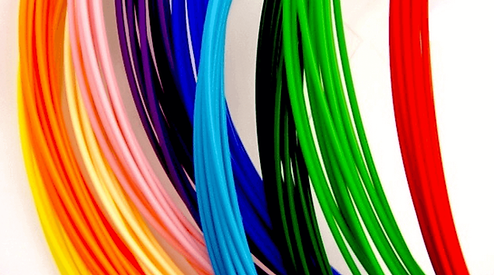
ABS
> Chemical composition and synthesis
Acrylonitrile–butadiene–styrene (ABS) is a thermoplastic polymer. It is a terpolymer forming two phases where the matrix (continuous phase) is composed of SAN (styrene-acrylonitrile) copolymer with dispersed particles of butadiene. The proportions of the three monomers (acrylonitrile, polybutadiene and styrene) can vary. Styrene is the main component, between 40 and 60 %. Butadiene and acrylonitrile amounts can vary between 5 to 30% and 15 to 35% respectively. With different compositions, ABS can achieve a wide range of chemical, mechanical, flow and impact properties. It can be assumed that styrene contributes to the rigidity and processability, acrylonitrile to the chemical resistance and butadiene (the rubber phase) to the toughness. However, the mechanical properties (mainly impact resistance and toughness) vary with temperature, ABS is commonly used between -20°C and 80°C. ABS is flammable at high temperature and can be damaged by sunlight. [6]


> Properties
ABS has a light weight (density: 1.06-1.08 g/cm³). It is an amorphous polymer so it has no melting point. However, the extrusion temperature is often assumed to be 220°C-230°C. Its glass transition temperature is 106°C [7][9].
Regarding the mechanical properties of FDM 3D print ABS, they may vary with the printing settings such as raster angle and gap (distance between two adjacent deposited filament in the same layer). Dawould and al [1] suggest a tensile strength between 30 and 35 MPa, a flexural strength between 40 and 65 MPa, an impact strength between 20 and 40 kJ/m2 (values obtained with FDM). However, since ABS is extensively used, there are different types to improve the properties such as biocompatible ABS or ABS-plus with better mechanical properties. Regarding the latest, Nunez and al [2] have obtained, with FDM printed ABSplus, 33 MPa as ultimate tensile strength, 58 MPa and 35 MPa as flexural strength (depending on the axis) and 6% of elongation at break. At the best of my knowledge, the chemical composition of ABSplus is not given, but higher mechanical strength (such as impact and flexural strength [2]) suggests more butadiene, the rubber component.
The chemical resistance, especially against corrosive agent, of ABS is enhanced thanks to acrylonitrile. It is partially soluble in acetone ( since the SAN copolymers are and not the polybutadiene ). It is insoluble in water.[8]
> As printing material
In order to avoid warping, it is required to heat the build plate at 110-130°C. It adheres well to PET or Kapton tape in this condition. It is also preferable to keep the printer walls closed to avoid that the ABS cools during the printing. ABS is well suited to mechanical design with interlocking pieces. It is possible to weld the different pieces with few drops of acetone. Acetone can also be used to improve the finishing. The extrusion temperature is around 220-230°C. [5]
> Applications
ABS is used in a lot of household appliances, musical instruments (ex: clarinet), golf club heads, keyboard keycaps... But the most famous application is the Danish toys “Lego”.
> Bibliography
[1] Michael Dawoud, Iman Taha and Samy J. Ebeid, Mechanical behaviour of ABS: An experimental study using FDM and injection moulding techniques, Journal of Manufacturing Processes, Vol 21, January 2016, Pages 39–45.
[2] P.J. Nuñez, A. Rivas, E. García-Plaza, E. Beamud and A. Sanz-Lobera. Dimensional and Surface Texture Characterization in Fused Deposition Modelling (FDM) with ABS plus. Procedia Engineering
Vol 132, 2015, Pages 856-863
[3] Acrylonitrile-butadiene-styrene (ABS) Production and Manufacturing Process, 18 October 2007 00:00, https://www.icis.com/resources/news/2007/10/18/9071053/acrylonitrile-butadiene-styrene-abs-production-and-manufacturing-process/
[4] Synthesis of Acrylonitrile Butadiene Styrene (ABS) Polymers, Saturday, 23 August 2014,
http://textileinsight.blogspot.be/2014/08/synthesis-of-acrylonitrile-butadiene.html
[5] Makerbot, ABS filament https://store.makerbot.com/filament/abs-large/
[6] D. M. KULICH, S. K. GAGGAR, V. LOWRY and R. STEPIEN, ACRYLONITRILE–BUTADIENE– STYRENE POLYMERS, ACRYLONITRILE AND ACRYLONITRILE POLYMERS (Vol 1), Encyclopedia of Polymer Science and Technology, p174-203
[7] Jin Zhu, Yufei Hu, Yijing Tang, Biao Wang, Effects of styrene–acrylonitrile contents on the properties of ABS/SAN blends for fused deposition modeling, Journal of applied polymer sciences, 2016
[8] HIDE0 KUBOTA Flow Properties of ABS (Acrylonitrile-Butadiene-Styrene) Terpolymer, JOURNAL OF APPLIED POLYMER SCIENCE VOL. 19, PP. 2299-2308 (1975)
[4]
[4]
> Experimental characterisation
As printing test, a standard dogbone shape has been 3D printed.
For the first test, the printing settings were:
- Extrusion temperature: 230°C
- Heated bed temperature: 110°C
- Print speed of 40 mm/s outlines and 90 mm/s for infill (100%).
- Closed printer (to avoid cooling of ABS during printing).
- Print platform covered by Kapton tape (polyimide tape).
- Dogbone printed on breakable support.
However, due to the strong warping, the printing couldn’t be achieved.
To avoid the warping during the second printing, the bed was heated up at 130°C. Nevertheless, the result was still not satisfactory.
For the third attempt, instead of “normal” ABS, ABS easyfil was used. ABS easyfil is known for its lower tendency to warp. The dogbone obtained is visible on the pictures below.
>> Printing test


ABS easyfil is then a promising material to achieve high quality printings. Moreover, the printing is relatively fast (20 minutes for a dog bone 100% infill) and no previous drying is required (ABS is mildly hygroscopic [6]). The easiest printing of ABS easyfil compare to standard ABS could be explained by a higher content of SAN. In fact, SAN increases the adhesion of ABS. [7]
>> DSC
We performed a DSC test on ABS before and after printing in order to see if the thermal properties of the polymer were altered by the printing. Our results are available on this page.
>> Rheometry
The different equations linked to the graph are:
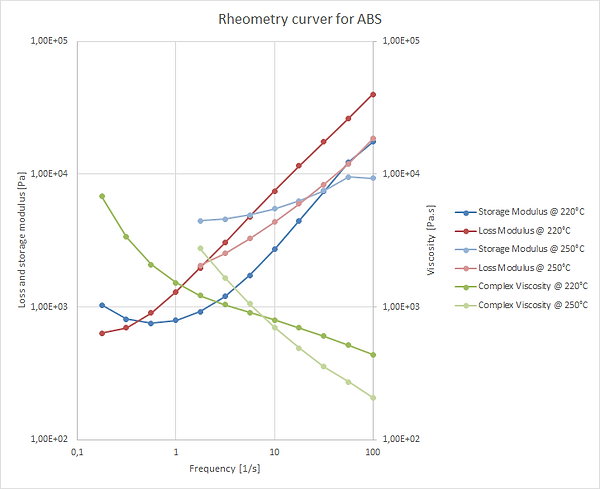

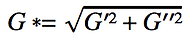
with G’ the storage modulus and G’’ the loss modulus
with η* the complex viscosity and ω the frequency
Concerning the viscosity, it can be observed that the viscosity decreases when the frequency increases. It means that the ABS is more liquid and flows more easily at high frequency.
The significant increase in viscosity at frequency lower than 1 Hz is due to the increase of the storage modulus and the loss modulus plateau.
The storage modulus increases at low frequency is not a physical phenomenon. A plateau could have been explain by some crosslinking points that can’t relax. Since it is not a plateau but an increase, the phenomenon is chemical. There are two possible explanations: either a degradation of the polymer, or the formation of new crosslinking points. In the case of ABS, a degradation seems more plausible.
The loss modulus plateau (reached between frequencies 0.1 and 1) is explained by the fact that a part of ABS does not flow. This part can be estimated at 10 % if we assume that the loss modulus would reach its high frequency plateau around 10^5 MPa. According to the structure of ABS and composition percentage, this is the polybutadiene bakcbones which do not flow. In fact, the viscosity of ABS is determined by the amount of SAN as continuous phase.[6]
​
Controlling the degree of grafting is a way to control the flow properties of ABS. The higher the amount of grafted polybutadiene, the higher the melt viscosity.
Important factors about ABS related to its process in 3D printing, are its high viscosity and the dependance of the latest in temperature and printing speed.
The dependance in temperature is significative, in fact an increase of 20-30°C for the melt temperature reduce the melt viscosity of 30%. [6]
The measurements at 250°C are not very conclusive since ABS started very quickly to oxidize and the experiments had to be stopped.
> Conclusion
ABS is an interesting and well-known material for 3D printing. Its properties (toughness, chemical resistance…) can be tuned depending on the composition. But it is often a compromise between different properties. For instance, in order to increase the impact strength, the degree of grafting of SAN has to be higher. But then, the melt viscosity is also increased and the process is more difficult.
Although its mechanical properties seem sufficient for the drone application, the disadvantage of ABS is its limited resistance to heat.
>> Manufacturing process
ABS was introduced commercially in 1954, by Borg-Warner. The patent dates from 1948. The common polymerization route is the emulsion process [3]. In emulsion polymerization, the monomers are dispersed in an aqueous phase where initiator radicals are found. The result is a long chain of polybutadiene crisscrossed with shorter chains of poly(styrene-co-acrylonitrile) (SAN branches).
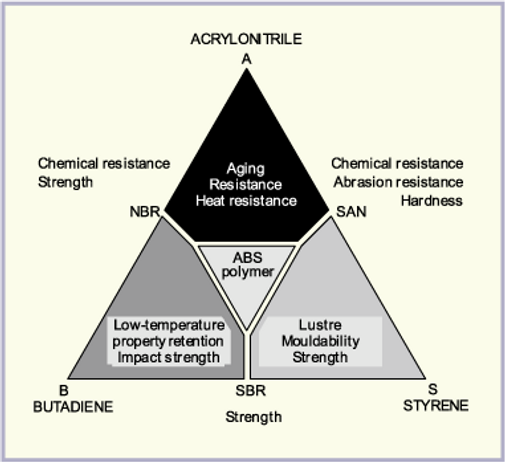
By Elisabeth