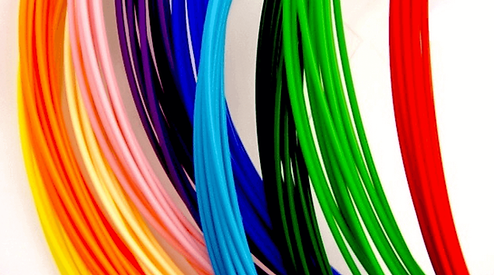
PVDF
1. Teng, H. Overview of the Development of the Fluoropolymer Industry. Applied Sciences 2, 496–512 (2012).
2. Ebnesajjad, S. in Applied Plastics Engineering Handbook 55–71 (Elsevier, 2017).
3. Wang, J. C. et al. Preparation and properties of poly(vinylidene fluoride) nanocomposites blended with graphene oxide coated silica hybrids. Express Polymer Letters 6, 299–307 (2012).
4. Lovinger, A. J. Ferroelectric Polymers. Science 220, 1115–1121 (1983).
5. Lolla, D. et al. Polyvinylidene fluoride molecules in nanofibers, imaged at atomic scale by aberration corrected electron microscopy. Nanoscale 8, 120–128 (2016).
6. Zhang, Q. m., Bharti, V. & Kavarnos, G. in Encyclopedia of Smart Materials (John Wiley & Sons, Inc., 2002).
> Bibliography
For this project, PVDF is an interesting material due to its mechanical properties and its thermal and oxidative resistance. Nevertheless, it is a very dense material compared to ABS, ABS-PC and other suitable materials and the fact that polar solvent can swell PVDF makes its use in humid environnement questionable.
> Applications
When using PVDF filaments the extrusion temperature should be around 210-215°C and a heated bed at 120-125°C is recommended. The usual printing rate for this material is 10 mm/sec.
> As printing material
> Properties
As other fluoropolymers PVDF has excellent chemical and physical properties, like having thermal and oxidative stability and weatherability (1-3). However, some polar solvent (ethyl acetate and acetone) can make this polymer swell. Compared to the other fluoropolymers PVDF has greater mechanical resistance. This material passes several crystalline forms depending on how it is synthesized. Combined with its dipole moment of 2,1 this polymer has one of the strongest piezoelectric properties amongst polymers (4, 5). Its average melting temperature is 170°C and it has a density of 1.78 g/cm3 denser than most of 3D printing polymers but less than polytetrafluoroethylene (Teflon) (6).
Polyvinylidene fluoride (PVDF) has been discovered in 1948 and was first commercialised by Pennsalt (now called Arkema) in 1961 under the brand name Kynar. It is made by free radical polymerization of 1,1-difluoroethylene usually through a suspension or emulsion method (1, 2). The structure of the monomer and the polymer are given by Figure 1.
> Chemical composition and synthesis

Figure 1: Polymerization of PVDF using 1,1-difluoroethylene. From (1).
> Conclusion
Some examples of application for PVDF are microfiltration membranes, microwave transducers, wire and cable coating, as build material for valves, pumps and bearings due to its chemical resistance and numerous other applications related to its piezoelectric property. (1, 3)
by Arthur