
Fused Deposition Modelling
Among the vast choice of 3D printing techniques, we decided to use the Fused Deposition Modelling (FDM) technique for our project. This technology is based on the deposition of layers of materials one after the other.

> How does it work ?
​
The principle behind FDM is quite straightforward: a thermoplastic material is melted and then extruded through a thin and heated nozzle. The nozzle can move both horizontally and vertically, thus creating a pattern defined beforehand by the adequate software.
In a little more details, the thermoplastic material is fed to the extruder in the form of a filament, wound around a spool. The filament is heated past its glass transition temperature and softened or melt inside the extruder (depending if the material is amorphous or (semi-)crystalline). The softened material then flows from a nozzle, which is positioned in such way to form, layer by layer, the desired object. The image on the left illustrates this principle perfectly and enables a clear understanding of the concept.
Image from 3dprintingforbeginners.com
The thickness of the deposited layer varies with the used material but generally ranges from 0.18 to 0.25 mm. Any geometry can be printed thanks to the use of a support structure. Support is needed in case of overhang, meaning when the printed layer is meant to rest on air. As printing on air is impossible (because the laws of physics still apply inside a 3D printer), a support structure is necessary. This structure is build such that it can be easily removed using for example a knife.

Image from materialise.com
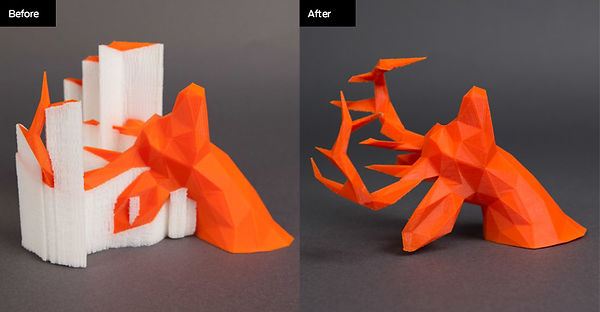
The support structure can also be build in another material, which can be selectively dissolved in water or in another solvent once the printing is done. 3D printing using two different materials is enabled by the use of a dual-extruder: this means the chosen material goes through one extruder, while the solvable material is fed to the other extruder.
Image from makerbot.com
> Pros and Cons
​
FDM was developed to print ABS, which is known for its good mechanical properties and its excellent durability over time, but is now available to a wide range of materials (see Materials section). Post-processing of the printed objects also does not cause any problem.
Another advantage of this technique is that FDM printer are commercially available, rendering it a very accessible technology. Not only are the printers and the needed materials affordable, they are also easy to use.
​
There are however some disadvantages to this technique. The first concerns the accuracy of the printing, especially when using lesser quality printers. For example, the standard accuracy is ± 0.15% (with lower limit on ± 0.2 mm) for high quality FDM printers. Loss of accuracy can for example be related to shrinking of the material upon printing. Through the layer-by-layer deposition of the plastic, parts also may exhibit an anisotropy in the Z-direction. Finally, this deposition technique results is step-structured surface and prevents the printing of fine details.
> Materials for FDM
​
Lots of common materials are available to print when using FDM. This feature contributes clearly to the popularisation of the method when dealing with 3D printing. The materials of interests are the common ABS, PLA, PC, nylon, etc, offering a very wide use of FDM.
The material is chosen depending on its intrinsic properties and the requirements that the printed object has to meet. It is also essential to be aware of the printing conditions when choosing a specific polymer, such as the extrusion temperature and the heated bed temperature.
> Bibliography
​
-
"A Comprehensive Introduction to 3D Printing Technology", 3dprintingforbeginners.com, accessed on 26/02/2017
-
Elizabeth Palermo, "Fused Deposition Modeling: Most Common 3D Printing Method", lifescience.com, accessed on 26/02/2017
-
Materialise, "Fused Deposition Modeling", http://www.materialise.com, accessed on 26/02/2017
​
By Roselien