Limosolve
> Chemical composition and synthesis
The High impact polystyrene (HIPS) is a thermoplastic heterogeneous polymer formed by addition of an elastomer (usually polybutadiene, figure 2) to polystyrene, an aromatic compound (figure 1).
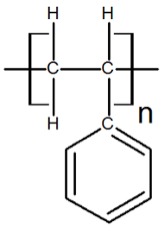

Figure 2 : Polybutadiene -(H2=CH-CH=CH2)n- [2]
Figure 1 : Polystyrene -(CH2-CH(Ph))n- [1]
HIPS has been first created by Ostromislensky in 1927 [3], to improve the properties of polystyrene. Indeed, it has a high tensile strength and optical clarity but is brittle, which limits the possible industrial applications. [4]
HIPS is commonly produced by “continuous bulk or bulk suspension processes, in which butadiene-based elastomer is first dissolved in styrene monomer, and the resulting mixture is then heated so that the polymerisation proceeds either thermally or with the aid of a chemical initiator”[3] . During the process, the continuous phase is first a solution of rubber in styrene, with discrete polystyrene particles that precipitates out of the solution. At some point during the polymerisation, a phase inversion occurs. The final material obtained is a continuous polystyrene matrix containing dispersed polybutadiene particles (the minor component of the polymer) of 0.5-6 μm grafted with polystyrene side chains [3][6]. These compartmentalized regions are obtained because, even if a copolymer is formed, polystyrene and polybutadiene are immiscible. Figure 3 shows the typical obtained HIPS morphology, where the polybutadiene appears in black, which occurs due to a complex interaction of process condition, thermodynamic factors and kinetics. The rubber content is typically 4-8 wt% [3].

Figure 3 : Typical solution-polymerized HIPS morphology (polybutadiene in dark) [6]
The chemical interaction created (thermally or with the initiator) between the two phases increase the toughness (impact resistance) of the polymer, due to the stress relaxing action of the polystyrene particles [4]. Impact strength increases with the polystyrene phase volume. The addition of rubber causes also an increase of the elongation, the ductility and the stress crack resistance, but it engenders a loss of clarity and a decrease in tensile strength and modulus [6].
> Properties
The HIPS is an interesting industrial material because it has the following properties : low cost, high machinability, good impact resistance, good dimensional stability. Also, it can be easily painted, sanded or glued [8][9]. It is safe to human and animals, but releases fumes upon heating which can irritate lungs and eyes. Therefore, the 3D printing should occur in a well ventilated room [5].
Regarding 3D printing, its properties are similar to ABS, but it has a superior hardness and impact resistance. It is a light filament, with a density of 1.06-1.08 g/cm³. Its melting point is approximated to be in the range of 180-260°C, even if it has no true melting point because it is amorphous. The product specifications of the HIPS (limosolve) filament can be found in the datasheet published by FormFutura [7] and are summarized in Table 1.

Table 1 : Properties of HIPS
> As printing material
As a 3D printing material, the HIPS became popular with the invention of the dual extruder 3D printing. Indeed, the HIPS is soluble in limonene, which makes it an interesting support material for ABS, PC, PLA and PC-ABS, allowing the impression of 3D models which were previously impossible [9]. The dissolution takes between 2 hours and 3 days, and is accelerated if the object is continuously shaken. The recommended extrusion temperature is 235 °C and should stay between 220°C and 260°C.
The contraction of the HIPS when it is cooled induces internal stress at the interface between the printed layers or the printing bed surface. Therefore, to avoid adhesion problems or curling, the entire object is required to stay at a temperature close to Tg during the 3D printing and to be cooled entirely after. So, is recommended that the 3D printer stays closed during the whole process. Moreover, the printing speed is recommended to be 40 mm/s and the printing bed is advised to be heated at a temperature of 110-120 °C [9]. The use of Kapton tape, Elmer’s glue or Blue tape can also be helpful.
> Applications
Thanks to its interesting properties, low cost and high machinability, the HIPS is used for a wide range of application as machined prototypes, production of toys, food processing application, cover, packaging or home appliance. Besides, it is used in both injection molding and extrusion processes, depending on the polymer’s viscosity.
> Experimental characterisation
The 3D printing test was a dogbone shaped object. The parameters used can be found in table 2. The printing was realised with blue tape, enclosure, and without drying. A first test was realised with raft which was difficult to remove. Therefore, a second printing without raft was made and can be observed in figure 3. In both cases, the adhesion was good and the sample presented no warping, the printing was easy and the result is satisfactory.
>> Printing test


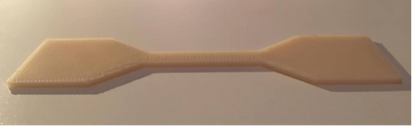
Table 2 : Printing parameters
Figure 3 : dogbone shaped printing test
>> DSC
A differential scanning calorimetry (DSC) experiment was performed on a HIPS sample, which had been dried in an oven at 60°C overnight. It this experiment, the polymer was progressively heated from 25°C to 300°C in order to observe its thermal behaviour. The graph obtained is presented on figure 4. This curves is very different from the one encountered in literature [10]. Indeed, it should only present one shift in baseline around the glass temperature. This could be due to the experimental errors of the machine. However, if the graph is looked at, three peaks that characterise endothermic transitions can be observed, around 30°C, 90°C and 245°C. The first one, around 30°C, is assumed to be due to the onset of the experiment and will be neglected
Then, a shift in the baseline can be observed between 80°C and 100°C. It corresponds to a step change in the heat capacity and indicates the glass transition temperature Tg. As the discontinuity is not pronounced, it does not allow to determine precisely the value of Tg. However, the temperature given by the datasheet of the material, 89°C, is situated in the the observed interval.
Finally, a third peak at 245°C can be seen. As the HIPS is known as amorphous, it is unexpected. It could either correspond to thermal degradation of the polymer; or to experimental errors.
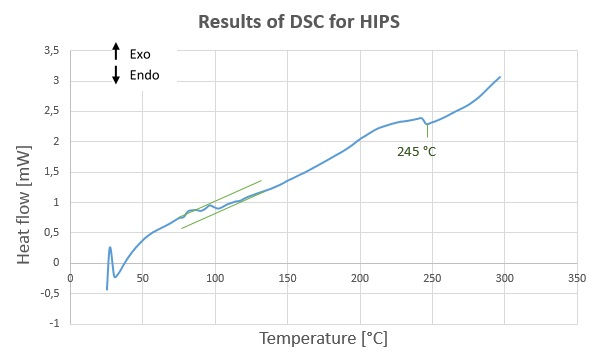
Figure 4 : Results of the DSC of an HIPS sample
>> Rheometry
A rheometry experiment was performed on a HIPS sample, which had been dried in an oven at 60°C overnight. During this experiment, a sinusoidal shear stress with varying angular frequency was applied to the material. The measure of the response in deformation allows us to study the viscoelastic behavior of the polymer. Indeed, the equations 1 is obtained and shows that the shear stress and the linear deformation are linked with two modulus, G’ and G’’ (γ is the linear deformation, ω is the angular speed and τ is the shear stress). G’ is called the storage modulus, and characterizes the elastic response of the material, which is the stored energy during the deformation. G’’, the loss modulus, describes the viscous response, which corresponds to the dissipation of energy and so to the flowability [11]. The complex viscosity can be deduced from these two moduli, as can be seen in equation 2.
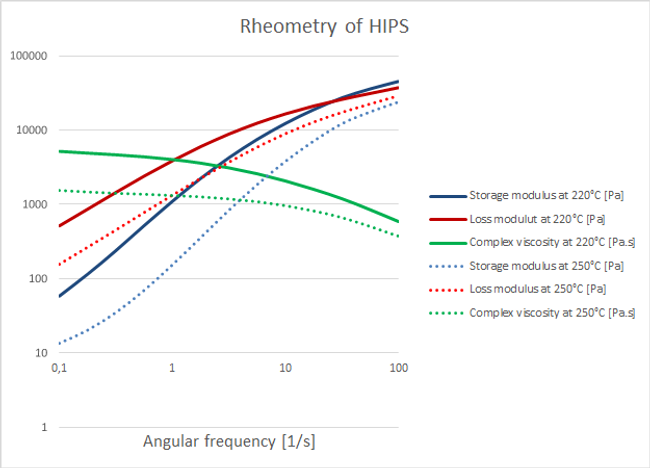
Figure 5 : Results of the rheometry of an HIPS sample
[1] ]”Les polymère”, http://physique.vije.net/1STI2D/index.php?page=polymeres_1, accessed on 25/03/17
[2] “Polybutadiène”, https://fr.wikipedia.org/wiki/Polybutadi%C3%A8ne, accessed on 25/03/17
[3] E. Saldivare-Guerra and E. Vivaldo-Lima, “Polymer synthesis, characterization, and processing”, 2013, Wiley
[4] J.R. Wunsch, “Polystyrène : Synthesis, Production and Applications”, 2000, Rapra Technology LTD. pp 20-22
[5] Yessica G., “Understanding HIPS, 3D printing filament”, http://3dpnexus.com/hips-3d-printing-filament-explained/, accessed on 12/03/17
[6] Mark, Bikales, Overberger and Menges, “Encyclopedia of polymer science and engineering”, volume 16, Wiley, 1989, pp 88-97
[7] ”LimoSolve Sample”, http://www.formfutura.com/formfutura-limosolve-sample.html, accessed on 12/03/17
[8] Plastincsintl, “HIPS (High Impact Polystyrène”, https://www.plasticsintl.com/datasheets/Polystyrene.pdf, accessed on 12/03/17
[9] ShapingBits, “HIPS 3D Printing”, http://www.shapingbits.com/3D-printing-guide/hips-3d-printing/, accessed on 13/03/17
[10] The material analyst - Determining coposition, https://www.plasticstoday.com/content/materials-analyst-part-33-determining-composition/2155122771576/page/3/1, accessed on 12/03/2017
[11] Polymer Chemistry, second edition, P. C. Hiemenz and T. P. Lodge, CRC Press, Boca Raton, 2007, 587 pp.
[12] Time-Temperature Superposition - A Users Guide, J. Dealy and D. Plazek, http://pages.mtu.edu//~fmorriso/cm4655/DealyPlazekTimeTempSuper2009.pdf, accessed on 24/04/2017
[13] “The principle and applications of Cox-Merz rule”, TA Instruments, https://www.researchgate.net/file.PostFileLoader.html?id=55a6902c5dbbbdbb628b45dd&assetKey=AS%3A273813168689157%401442293555131, accessed on 30/04/2017.
​
> Bibliography


Equation 1 Equation 2
A frequency sweep was first realized at 220°C and then at 250°C. The logarithmic graphs obtained are presented in figure 5. The interesting frequency are situated between 0.1 and 1 Herz, because the printing speed is superior to 1 mm/s.
The curves of the loss modulus (G’') and the storage modulus (G') are considered in this range of frequency. When G’’ is superior to G’, the energy given to the polymer is dissipated, and the material flows. This is the thermal domain of relaxation. At 220°C, it occurs around 30 [1/s], which is higher than the frequencies of interest. As can be seen, below that point, the slope of G’ is close to two and the slope of G’’ is close to one (perfect flow). It can be concluded that the HIPS is nicely flowing during 3D printing, and will then form surfaces which are smooth and even, which makes it a suitable support material. It would have been interesting to carry out the experiment at lower temperatures to observe when the temperature would be too low for a good 3D-printing. Moreover, the crossover occurs when the frequency is equal to the inverse of the relaxation time, which is the times it takes the polymer chains to return to their equilibrium position after being disturbed. A value of 0.034 seconds is obtained.
When comparing the curves at different temperatures, it can be seen that their shape is similar. This is the time-temperature superposition principle, which states that the curves of G’ and G’’ are shifted to the right (higher angular frequency), with the increase of temperature [12]. So, the relaxation time is lower when the polymer is heated.
Regarding the viscosity, it can be observed that it is constant in the range of the appropriate frequencies. Then, it slowly decreases at both temperatures, meaning that the flow state become non-newtonian. Therefore, a small change in the printing speed will not induce large changes in viscosity, which makes HIPS a reliable 3D printing material.
Finally, the cox-Merz [13] can be used to observe the variation of steady state shear viscosity with the shear rate (which was kept constant in our experiment). Indeed, it says that this curves is similar to the one of the complex viscosity in function of the frequency, shown here on figure 5. The two curves have a plateau followed by a decrease at the same point, which is 29.4 Hz, the inverse of the relaxation time. Therefore, it means that shear-thinning, which is the decrease of viscosity with the increase of shear rate, will occur during 3D-printing above that point.
High impact polystyrene combines the properties of stress relaxation from the butadiene with the high tensile stress of polystyrene. It is easily printed, reliable and is dissolvable in limonene. It benefits from good flowability properties at the printing temperature, which makes it a popular support for complex printing with dual extruders. As its thermal printing condition are similar to ABS, it will be used as a support material for our done if needed.
> Conclusion
By Marine