
FlexiFil
> Chemical composition and synthesis
FlexiFil belongs to the thermoplastic elastomer (TPE) family. More precisely, it is a thermoplastic copolyester elastomer (TPC or TPE-E), sometimes referred to as thermoplastic rubbers. It is a class of copolymers.
Thermoplastic copolyester elastomers (TPE-E) are semi-crystalline thermoplastic elastomers. They are synthesized by polycondensation of dimethyl terephtalate (DMT) with a short and a long chain diol. The diols commonly used are the butanediol (BDO) and polytetramethyleneoxide (PTMO). As a result of the polycondensation, a multiblock copolymer of polybutylene terephthalate (PBT) and PTMO is obtained. [3] The process is depicted on the figure below.
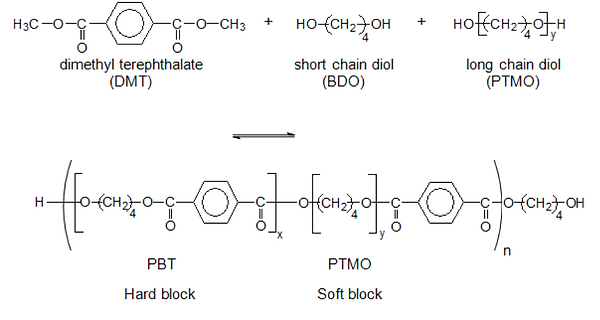
The hard blocks, rearranged in a crystalline structure, present the characteristics of a hard thermoplastic, while the soft block, arranged in an amorphous phase, behave much like an elastomeric polymer.
> Properties
TPE-E is a class of polymer presenting both thermoplastic and elastomeric properties, so it presents structural strength, but also exhibits elasticity. FlexiFil combines two Tg at about -44°C and 52°C, obtained by DSC measurements on FlexiFil samples, roughly corresponding to the glass transition of the soft block (PTMO) (Tg = - 52°C [11]) and the hard block (PBT), (Tg = 60°C [12]) respectively. It also possess and a melting temperature Tm (180°C), that makes it usable in a very broad temperature range.
​
At room temperature, the nodules composed of hard segments are in the crystalline phase, but the amorphous phase composed of the soft segment is in a rubbrey state (viscous liquid state). This way it presents some flexibility. Because the nodules of crystalline phase are dispersed in the continuous amorphous phase, the polymer can be easily elastically deformed thanks to the rubbery behaviour of the amorphous phase. The copolymer in its entire mass will become a fluid at a sufficiently high temperature.
The material exhibits excellent fatigue resistance and the ability to recover its shape after being deformed. It possess a tensile strength (stress at break) of 24 MPa, a tensile modulus of 95 MPa and an elongation at break about 530%. It has a density of 1.15 g/cm3. [7] Moreover, these thermoplastic elastomers present excellent chemical stability when being exposed to non-polar solvent such as greases and oils. They are also very resistant to UV light. [5]
Finally, TPE-E materials have the potential to be recyclable, which is not the case for traditional rubber compounds. [6]
Figure 1 : Process for the creation of a thermoplastic copolyester elastomer.
> As printing material
FlexiFil is easily extruded, which makes it an ideal polymer to be printed. Predrying of the FlexiFil filaments is recommended. It is also recommended to lower the printing speed (compared to printing speed of ABS or PLA) to 10-20 mm/s.
Some efforts have to be done in order to have a good first layer adhesion. Blue Tape can be combined with glue stick in order to improve the adhesion. Also, the recommended heated bed is about 60-100°C. [1]
​
The rubbery characteristics of the filament can cause some friction in the bowden tube of the printer. In order to avoid some problems with the feeding of the extruder, some lubricant can be used in the bowden tube. [5]
> Experimental characterisation
The printing test of the FlexiFil consisted of a dogbone, usable later in order to perform mechanical tests for a better characterisation of the FlexiFil properties. The dogbone was printed on a raft for a better adhesion. The printing conditions were the followings :
- Extrusion temperature : 230°C,
- Bed temperature : 70°C,
- A slow printing speed about 20 mm/s,
- Blue tape lied on the bed also for a better adhesion,
- The polymer was dried.
As can be seen on the picture below, we can observe a non-negligeable warping of the dogbone.
>> Printing test

Figure 3 : Dogbone in FlexiFil, obtained for the printing test.
Print flexible filaments is generally not an easy task, and warping is frequently obtained. Some parameters can be optimized in order to obtain a better printing. These modifications will be setted up if FlexiFil is used for the final drone.
The modifications are given by the manufacturer or found on some blogs, and can be [1] [8] :
- Pre-drying of the polymer filament,
- Use of combination of glue and blue tape,
- Print much more slowly (5-10 mm/s),
- Adjust the bed temperature.
> Applications
Thermoplastic elastomers are used where the needs go beyond the properties proposed by conventional elastomers. TPE-E have a broad range of applications, from automotive sector (e.g. in snowmobile tracks, where abrasion resistance is at premium) to medical field (where the softness offered by TPE-E is ideal for the catheters). [5]
Also, thanks to their flexible properties and the facility to be printed, TPE perfectly found their application in bioengineering and 3D printing, such as for the use in customized tissue engineering. [2]
Finally, it is relevant to mention that TPE can also be used in electronic to print flexible electronic devices; which has a promising future.
>> DSC
>> Rheology
​
In order to more deeply determine the properties of the FlexiFil, a rheometry study on FlexiFil samples was performed. The rheology of materials permits to obtain the mechanical properties of materials that present a viscoelastic behavior. It is well suitable for melt polymers.
On the graph presenting the storage and loss modulus of the FlexiFil, Figure 4, it can be observed that the behavior of the G’ and G’’ curves in the range from 1 to 100 for the angular frequency follows the expected shape for small angular frequencies (see the first graph of the « rheometry » section of the nGen Colorfabb material). This way, the polymer flows correctly. The last divergent points of the red and green curves can be seen as noise of the rheometry measurements.
It is also noticed that the loss modulus G” possess lower values when temperature increases: the blue curve of the loss modulus (245°C) is situated below the curve of the loss modulus at 217°C and 220°C. Also, the curves of the storage modulus correspond to lower modulus value when temperature increases, and so the storage modulus G’ decreases with increasing temperature. This way, the melt polymer loses the elastic and viscous components of its total response when temperature increases. Indeed, at 220°C the FlexiFil is a viscous liquid polymer (this temperature exceeds the Tg of the two phases and the Tm of the crystalline one: the crystalline phase is molten, and the amorphous phase is more fluid than viscous), as can be seen on the DSC results.
Using the time-temperature superposition principle, it is possible to shift these curves horizontally by a shift factor, until they overlap to produce a master curve that presents the modulus values on a higher range of frequencies, for a reference temperature. This principle permits to obtain values of modulus, for a specific temperature, at frequencies for which rheometers are not able to measure the response of materials. [10]
[1] “FlexiFil Sample”, http://www.formfutura.com/formfutura-flexifil-sample.html, accessed on 10/03/2017
[2] A. Przybytek, J. Kucinska-Lipka, H. Janik, Thermoplastic elastomer filaments and their application in 3D printing, Elastomery, nr. 4, pp. 32-39.
[3] "Thermoplastic Copolyester Elastomers", https://www.ihs.com/products/copolyester-ether-chemical-economics-handbook.html, accessed on 11/03/2017
[4] Holden, G., Elastomers, thermoplastics, Encyclopedia of Polymer Science and Engineering, vol. 5, Wiley, 1986.
[5] “Thermoplastic elastomer”, https://en.m.wikipedia.org/wiki/Thermoplastic_elastomer, accessed on 12/03/2017
[6] Plastic Europe, “Thermoplastic polyester elastomer (TPE-E)”, http://www.plasticseurope.org/what-is-plastic/types-of-plastics-11148/engineering-plastics/tpe-e.aspx, accessed on 10/03/2017
[7] FormFutura, “Technical Data and Information - FlexiFil”, https://static.webshopapp.com/shops/021593/files/053156996/tds-flexifil.pdf?_ga=1.134315313.1175835800.1489487523, accessed on 5/03/2017
[8] Pinshape Blog, “Top 5 Tips for Best Results with Flexible Filament”, https://pinshape.com/blog/tips-for-best-results-with-flexible-filament/, accessed on 23/03/2017
[9] Time-temperature superposition principle, Wikipedia, https://en.wikipedia.org/wiki/Time%E2%80%93temperature_superposition, accessed on 25/04/2017
[10] Paul C. Hiemenz, Thimoty P. Lodge, Polymer Chemistry, Second Edition, CRC Press, London, 2007
[11] James E. Mark, Physical Properties of Polymers Handbook, https://books.google.be/books?id=fZl7q7UgEXkC&pg=PA227&dq=Glass+transition+poly(tetramethylene+oxide)&hl=fr&sa=X&ved=0ahUKEwj7hNrm--LTAhXqDMAKHbo0C10Q6AEIJjAA#v=onepage&q=Glass%20transition%20poly(tetramethylene%20oxide)&f=false, accessed on 11/05/2017
[12] Polybutylene terephthalate, Wikipedia, https://en.wikipedia.org/wiki/Polybutylene_terephthalate, accessed on 24/04/2017
> Bibliography
We performed a DSC test on FlexiFil samples before and after printing in order to analyse if the thermal properties are degraded or not by the printing of the filaments. Our results are available on this page.


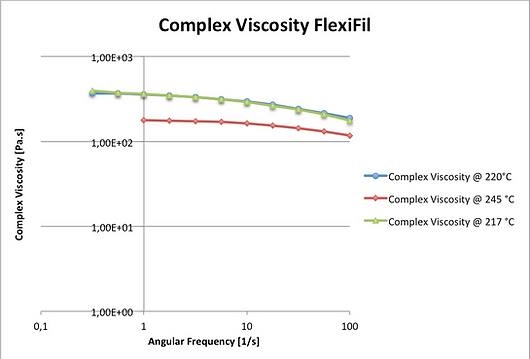
Figure 4
Figure 5 presents the complex viscosity measurements. The viscosity has lower values when temperature is increased. Indeed, the amorphous phase (viscous liquid) becomes less viscous and more and more fluid as temperature is increased. The viscosity is observed to be quite constant for a certain temperature. It means that the 3D printing (extrusion speed, change in printing speed, etc) does not influence too significantly the viscous response of the FlexiFil polymer.
Figure 5
Figure 6
The damping factor is defined as G''/G', or tan(delta). It is the direct ratio of the viscous and elastic parts of the modulus. Indeed, as the elastic response of the polymer to a dynamic strain is in phase with the applied strain and the viscous response appears only with a certain delay, said out of phase, we can write the dynamic modulus as


with Gm as
Delta is the phase angle. When , the material behaves like a liquid, and when the damping factor tends to 0, the material is solid-like. [10]

In the case of FlexiFil (see Figure 6) the damping factor at these temperatures being continuously above 1, it can be observed that the polymer will be more liquid-like than solid-like. It is advantageous if we recall that we need to obtain a flowing polymer in order to print the drone using FDM.
​
Rheometry measurements tell us that the mechanical properties of FlexiFil allow the filaments to flow adequately at the extrusion temperature (comprised between 220°C and 260°C) and so that FlexiFil is indeed a well adapted polymer for 3D printing by FDM.
By Grégoire
Thermoplastic copolyester elastomers such as FlexiFil are known as two-phase system: a crystalline phase, composed of the hard segments forming small crystal nodules, is dispersed in an amorphous phase composed of the soft segments of the polymer chains (rubbery elastomeric components). It is depicted on Figure 2. It seems that this structure of a continuous phase that exhibit elastic behaviour and a dispersed phase that represents the crystalline part is confirmed by the AFM analysis performed on FlexiFil samples.

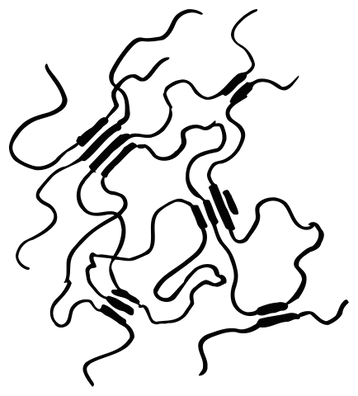
Amorphous phase (soft segments)
Crystalline phase (hard segments)
Figure 2 : Schematisation of the crystalline phase, composed of the hard segments, dispersed in a continuous amorphous phase composed of the soft segments of the FlexiFil chains.
> Conclusion
The FlexiFil filaments present lots of advantages as printing material for the flexible parts of the drone (bumpers,...). Its thermal properties meet the requirements and should permit to protect the drone from shocks even at relatively high temperature (120°C). The polymer is also relatively easily extruded, but its tendency to warp can be a real issue when printing some pieces. We can go beyond this issue by taking some precautions (use of blue tape for example) and obtain very effective bumpers for the drone. This is why we choose to use this polymer for the flexible parts of our drone.