Continuous Liquid Interface Production (CLIP)

Other 3D printing techniques
> How does it work ?
​
Continuous Liquid Interface Production is a technique which uses photopolymerisation to create 3-dimensional smooth-sided objects. The machine is made up of a liquid bath with a build platform above which is lifted continuously during the polymerisation. The liquid is an UV-curable resin which solidify in presence of light. To manage the printing, the UV images are successively projected through the bottom of the pool, made of a UV-transparent membrane. This membrane is also permeable to oxygen and is able to control precisely the amount of oxygen going through the liquid bath. The oxygen, in turn, acts as an inhibitor to the polymerisation and create a “dead zone” of a few microns, where the polymer stays in liquid state. This zone is situated just above the membrane, preventing the solidified resin to attached to it.

Image from 3dprint.com
> Pros and Cons
​
This method brings a solution to the major drawback of traditional 3D printers which is the slow speed (a few hours for small objects). It can print a hundred times faster small objects with consistent mechanical properties, within materials required for complex commercial quality products. Indeed, the fact that it is continuous eliminates the layers and so the mechanical defects. The surfaces are smooth and the properties are not dependant on the printing direction. The size of the object is however still a limitation due to the build platform (14cm*33cm*8cm for the first prototypes), together with the fact that this expensive printing technique is not yet spread in the market.
Selective laser sintering (SLS)
> How does it work ?
​
The SLS uses powder of usually polymer (nylon) but also ceramic or glass. This powder is spread in a thin layer on top of a plate by a roller (as can be seen on the image). A high power CO2 laser is controlled by a computer which tells it where on the powder the laser has to pulse in order to print the object. Indeed, it heats up just below the powder's sublimation point in order to fuse it into the solid 3D-object. Next, the platform goes down and a new layer of powder is added by the roller. The steps described above are repeated until the whole object is printed. Finally, the object is cooled down and the extra powder is removed.
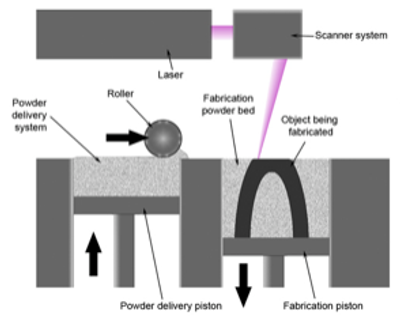
Image from 3dinsider.com
Stereolithography for 3D printing (SLA)
> How does it work ?
The basic components of such an apparatus are the liquid reservoir containing the resin, a moving platform on which the object is printed and a laser controlled by a computer through mirrors. When the laser makes contact with the resin, a chemical reaction occurs hardening the resin on a precisely located spot. The laser moved in the X and Y axis casting a layer of cured resin. Each time a layer has been cured, the platform is moved on the z axis. After printing, the object is washed of any resin excess through adapted solvent bath. Although a solid object is obtained, the conversion of active species from the resin is often incomplete and a post-curing with UV-light is recommended in order to improve the mechanical properties of the material. Lastly, this method allows to print the object in a bottom-up or top-down manner according to the apparatus used. In the second case the reservoir must have a particular UV-transparent window in order to cure the resin from the bottom, as shown in Figure 2.
Stereolithography method (STL), also called STA for stereolithography apparatus, was the first solid free forming system commercially available in 1986. Basically the technique is a layer-by-layer printer based on an UV-laser to cure a resin to a solid material. The process is called photopolymerisation. A schematic view of the apparatus is shown on the figure below.
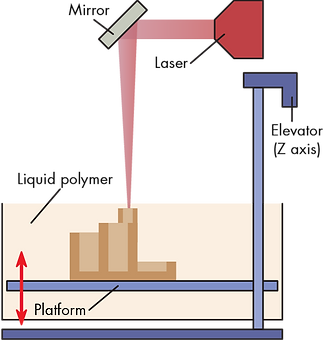
Figure 1: Schematic view of a STL printing device. From http://machinedesign.com/3d-printing/what-s-difference-between-stereolithography-and-selective-laser-sintering

Figure 2: Schematic overview of a bottom-up (left) and top-down (right) STL printers. From : http://www.sciencedirect.com/science/article/pii/S0142961210005661#
> Pros and Cons
The main advantage of SLS is that no support is needed to print complex shapes. Indeed, it is easy to remove the excess of powder which is then reclaimed back into the machine for the next print. Moreover, it is accurate and a large selection of materials can be used. However, this technique has some drawbacks too. The printed object can be porous and can have a rough surface. Some thermal distortion as shrinking or warping can also occur.
​
​
By Marine
By Julie
Bibliography
-
"Insights into Continuous Liquid Interface Production (CLIP) and Digital Light Processing (DLP) 3D Printers", additive3D.com, accessed on 26/02/2017
-
Brian Krassenstein, "Carbon3D Unveils Breakthrough CLIP 3D Printing Technology, 25-100X Faster", 3dprint.com, accessed on 27/02/2017
-
Joseph deSimone, "What is 3D printing was 100x faster ?", https://www.ted.com/talks/joe_desimone_what_if_3d_printing_was_25x_faster, accessed on 27/02/2014
-
Sculpteo, "3D Printing Material: Prototyping Acrylate CLIP Resin", https://www.sculpteo.com/en/materials/clip-resin-material/prototyping-acrylate-clip-resin-material/, accessed on 13/04/2017
-
Elizabeth Palermo, "What is Selective Laser Sintering?", lifescience.com, accessed on 27/02/2017
-
"How To 3D Print – Beginner’s Guide To 3D Printing", 3dinsider.com, accessed on 27/02/2017
-
"FDM vs SLS", Jack Wolf – 3D Support Specialist, http://mastergraphics.com/fdm-vs-sls/, accessed on 21/04/2017.
-
Advantages/disadvantages of selective laser sintering, https://powdertransport.wordpress.com/2014/03/02/advantagesdisadvantages-of-selective-laser-sintering/ , accessed on 21/04/2017.
-
LI, D.-., CHEN, J.-., YUAN, Y.-., HUANG, K. and FANG, H.-., 2015. Development and application of stereo lithography apparatus. Beijing Gongye Daxue Xuebao/Journal of Beijing University of Technology, 41(12), pp. 1769-1774.
-
https://pinshape.com/blog/fdm-vs-sla-how-does-3d-printer-tech-work/, 04/03/2017
> Pros and Cons
The pros of STL are the high accuracy, the speed, strongly chemically bound layers, printing elastomers (or other thermoset polymers), printing polymer-ceramic hybrids and the ability to print in two orientations (top-down or bottom-up).
The cons are the materials available (because of the use of resins as printing material), the post-printing treatments with cleaning the excess resin, removing the support material and curing the object in a UV-chamber. Moreover, the cost of SLA is higher than most FDM apparatus.[3]
For a detailed overview of a SLA printer, a video realized by Tested is presented bellow.
By Arthur