
NinjaFlex
Image from lulzbot.com
> Chemical composition and synthesis
The NinjaFlex is part of the TPUs (thermoplastic polyurethane) with elastomer segments. PURs (polyurethane) are generally synthesized by reacting diisocyanates and dialcohols therefore forming chains of urethane groups. This is illustrated by the figure representing a polyurethane structure with a marked urethane group.
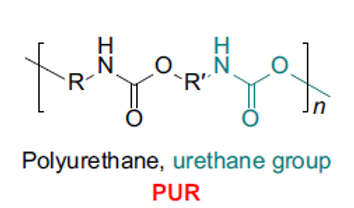
By alternating different copolymer blocks, it is possible to obtain flexible and stiff segments in the polymer chain. To obtain long and soft chains such as the ones that might be contained in the NinjaFlex, long diols are used in combination with a small contribution of diisocyanates. The TPU of the NinjaFlex wire is produced by extrusion. The Ninjaflex is a semicrystalline polymer. It possesses a Tg and a Tm. Under the Tg, the polymer is rigid, between the Tg and the Tm it is elastic and above Tm, the polymer melts.
[2]
> Properties
The NinjaFlex most important mechanical properties are its flexibility and its toughness. It can be extended from 36% (elongation at yield) up to 660% before breaking and allows repeated movements or impacts without wear or cracking. Its Young’s modulus is 12 MPa, tensile strength at yield is 4 MPa and ultimate tensile stress is 26 MPa. It possesses other interesting features as abrasion resistance (0.08g mass loss, 10,000 cycles) which is 20% better than ABS and 68% better than PLA. As composed of polyurethane, it reduces vibrations instead of transmitting them. The melting point is 216°C, the glass transition temperature -35°C. Moreover, it is chemically resistant to many liquids including naphtha, ASTM oils #1-3, petroleum and Freon. The Ninjaflex is not degraded by water for a short contact but a long exposure can alter its elastic properties through hydrolysis. Long exposures outside are not recommended because UV can degrade the Ninjaflex. Four to six month is the delay by which degradation can become visible.
> As printing material
The extruder temperature range is 225°C – 235°C, the plateforme must either be heated to 40°C or protected with blue painter tapes. The print speed for the top and bottom layers: 10-20 mm/ sec (600-1200 mm/ min) and for the infill speeds: 15-35 mm/ sec (900-2100 mm/ min). To connect printed parts, it is recommended to use plastic welders, soldering irons, wood burners or heat guns. it can be bound to other plastic using the same method.
> Applications
Several potential application are: Seals, gaskets, plugs, leveling feet, protective applications. These choices are motivated by the flexibility and the reliability of the NinjaFlex.
​
​
​
Example: a leveling feet where the bottom part could be made with ninjaflex.

> Experimental characterisation
The printing of the NinjaFlex can be difficult due to its flexibility. It is quite difficult to insert it in the extruder and need particular attention. In fact the extruder must be cleaned first by inserting another flexible polymer as the FlexFil in order to purge it. Otherwise, the NinjaFlex alone could meet problem to push remaining ABS from a previous usage of the printer. Once the NinjaFlex has been fed to the printer, the impression could proceed without other problems. It sticked to the printing bed, the final layer of the impression is not very clean, several white filaments remain.
>> Printing test

>> DSC
Differential scanning calorimetry is a technique which measures difference in heat flow between the sample and the reference. The heat flow diagram allows to identify changes in polymer materials. The heat flow is equivalent to the change in enthalpy over time :
The first term corresponds to the heat capacity of the sample. The second term corresponds to the endothermic or exothermic transition undergone by the product. During a glass transition, (glass to rubber) the specific heat capacity is shifted to a higher value. This phenomenon appears on the DSC trace as an inflection.
When the polymer is melting, it undergoes an endothermic change which appears as a negative peak on the DSC.

> Bibliography
-
Zaremba, D. & Evert, R. in Polymer Optical Fibres 153–186 (Elsevier, 2017).
>> Rheology (dynamic mechanical analysis)
The rheological analysis enables to study the viscoelastic properties of the material. The sample undergoes a periodic solicitation either at a periodic stress or a periodic strain. Both stress (sigma) and strain (epsilon) are recorded. For a purely classic material, both stress and strain are in phase. While for a viscoelastic material, there is a phase difference between the stress and strain.
​
The relation between the stress and strain can thus be represented by :
​
​
​
​
where E* is the complex modulus defined as where E’ is the in phase modulus or the storage modulus and E’’ is the out of phase modulus or viscous modulus.
​
The storage modulus measures the mechanical stored energy representing the elastic portion and the the loss modulus measures the energy dissipated as heat representing the viscous portion.
​
The higher the E”/E’ ratio= tan delta (known as the damping factor) the higher is the ability of the material to absorb shocks and vibrations.

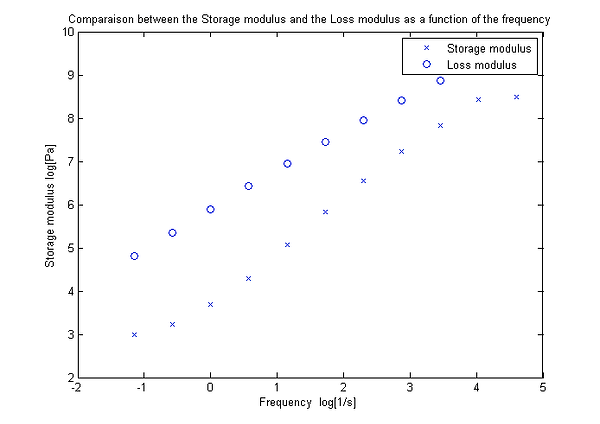
At low frequencies (below 1Hz), the storage modulus is low, around 10³ Pa conforming the rubbery (elastomeric) character of the polymer. At higher frequencies above 10^4 Hz, the modulus is significantly higher which means that the material is more rigid.
​
The material has a loss modulus higher than the storage modulus, this is typically the behaviour of a damping material. A damping material tends to reduce the vibration and to dissipate the energy of an impact into heat.
> Practical use for the drone
The NinjaFlex with its damping characteristics seems an interesting material for the bumpers of the drone. Its high deformability and ability to cancel chocs and vibration represents upshots. Now that we understand how we can print it and that it does not warp, thus providing a clean printing, we could use it efficiently.
> General description
The NinjaFlex is a formulated thermoplastic polyurethane, a type thermoplastic elastomer (TPEs). These polymers are the association of a thermoplastic phase and a rubber matrix. Fenner Dives, Inc was the one who introduced the Ninjaflex in 2014.The NinjaFlex can be deposited by fused deposition modeling (FDM), stereolithography (SL) and laser sintering. Among these different techniques, the FDM remains by far the most common deposition technique. The NinjaFlex is an interesting material due to the fact that it can be printed and possesses a great flexibility and elastic regime. (elongation at break up to 660%).

The DSC results are not very precise, this analysis is carried on the graph above. However we can see two different transformations occurring. One small inflection around -30C°, that can be seen both during cooling and heating ramps, which corresponds to the glass transition temperature. A negative peak around 215°C is the melting temperature. Those results are quite close to the Tg=-35°C and Tm= 226°C that were present in the literature.
A second DSC analysis was performed. Due to an improved calibration, the signal is more sensitive, see the figure below.
However, the thermo-mechanical history of the sample is unknown for the two DSC that were realised. The level of crystallinity and the size of crystals are not controlled. As a consequence, the DSC trace shows several peaks around 80, 140, 220, 240°C. In the temperature range between -35 and 50°C, the sample may undergo cold crystallisation. The glass transition can be seen between -50°C and -35°C.
To obtain a DSC trace with well defined Tg and Tm, it would be better to run a first heating ramp followed by a continuous cooling ramp before a second heating which would be analysed.
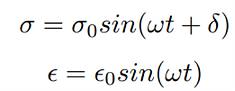

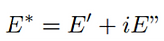
We can see that for all frequencies, the damping factor is superior to 1, this means that we have a damping material. In addition to this, a phase transition occurs when the material has its highest value of the damping factor. In our case the phase transition occurs at 1Hz. This transition is not the glass transition which is known to occur around -35°C. However, it must be a secondary transition associated to other movements of polymer chains enabling dissipation of energy.
By Brice

> Conclusion
The Ninjaflex is a thermoplastic elastomer which is easy to print. Its main advantages are its flexibility, its elongation at break (up to 660%) and its damping properties which make it suitable for bumper at room temperature. However at higher temperature, this might not be an appropriate choice for the drone because it would to viscous to be sure that the cones would conserve their shape in case of shocks. This is why another material which has a better resistance to temperature was chosen over Ninjaflex for the drone.