
Taulman645
> Chemical composition and synthesis
The nylon Taulman 645 is an improved version of Taulman 618 especially designed for 3D printing by Taulman3D. Indeed, industries wanted a nylon with a higher strength and easier to print than Taulman 618.
Nylon is a thermoplastic polymer and more precisely, an aliphatic polyamide. This means that it contains a repeating amide group. Moreover, nylon has a semicrystalline structure.
Taulman 645 is a variant of nylon 6 and nylon 6T (made by polymerizing hexamethylene diamine with terephtalic acid, more information) with a crystallinity optimization process [1]. Therefore, a focus on nylon 6 (the number 6 means that the respective monomer is composed of 6 carbons [2]) will be done. Its structure can be seen on Figure 1 below.

For the synthesis of nylon 6 which can be observed on Figure 2, a ring-opening polymerization is performed. First, water initiates the reaction by opening the monomer “ε-caprolactam” (cyclic) to form aminocaproic acid. Then, the reaction of addition of lactam on the growing chain takes place. At the same time, the condensation reaction happens where two chains react to form one longer polyamide chain [2][4]. More information about nylon 6 and its synthesis can be found here.
Figure 1 : Structure of nylon 6 [3].


Initiation:
Addition reactions:
Condensation reaction:

Figure 2 : Synthesis of Nylon 6 [4]
> Properties
The nylon Taulman 645 has a semicrystalline structure with some very interesting features improved from Taulman 618 for the 3D printing. Indeed, it is stronger (tensile strength of 114 MPa for Taulman 645 versus 66 MPa for the Taulman 618), less hygroscopic and easier to print than Taulman 618. Moreover, it is transparent and has better mechanical and thermal properties and is lighter (density of 1.08 g/cm³ at 21,5 °C) than other common 3D printing polymers as PLA and ABS. A summary of its properties can be found in the Tables 1 and 2 below [5][6][7]:
> As printing material
Taulman 645 is a material really appreciated by the 3D community thanks to its high strength, durability, bridging performances (ability to print in a gap between to points, more information) and transparency. Moreover, it is lighter and shows less shrinkage than ABS and PLA. The printing features for nylon Taulman 645 can be found in the Table 3 below [8][9].


Nylon Taulman 645 does not emit any fume or odor during printing. However, some steam can appear. It is needed to dry nylon before printing because it is hygroscopic. The main drawback of nylon is that it is really difficult to use for dual-printing. This is due to the self-lubricating properties and chemical resistance of nylon. [10]
> Experimental characterisation
A 3D printing of a dogbone-shaped sample was performed. As the nylon is hygroscopic, the polymer had to be dried before the printing. This was done by putting the polymer in a vacuum oven at 60 °C during one night. Then, the parameters of printing are collected in the Table 4 below. The printing was realised with the cover of the printer to let the polymer cooling down slowly and a raft was used to avoid any warping of the object. Finally, the printing bed was covered with blue tape for the adhesion of the printed object.
>> Printing test
The result can be observed on Figure 3. Some warping of the sample can be noticed. Moreover, due to the high strength of nylon, it was really difficult to remove the raft. A second 3D-printed dogbone shaped sample was realised with a higher bed temperature (80 °C) and without raft. The result can be seen on Figure 4 but warping is still present.
>> DSC
A DSC was performed on a sample of Taulman 645 to analyse its thermal behaviour. For this experiment, a temperature ramp between 25 °C and 300 °C was used. As the nylon is extremely absorbing moisture, the sample was dried (overnight at 60 °C) before the experiment. The result of the DSC is reported on Figure 5. On this curve, two peaks can be observed which correspond to endothermic transitions. However, the first peak is neglected.
​
Figure 3 : printed dogbone shaped with raft.


Figure 4 : printed dogbone without raft.
Next, no glass transition temperature (Tg) can be seen on this graph. Indeed, it is represented by a change of slope in the curve which corresponds to the heat capacity difference of the sample before and after the transition. [11] However, nylon Taulman 645 is a semicrystalline polymer which means that a glass transition temperature is expected. Indeed, a glass transition temperature of 52 °C can be found in the literature for this material. [5] This can be explained by a high crystallinity degree with a too low sensibility of the device, or a confined amorphous phase, etc.
Then, as the nylon is a semicrystalline material, a cold crystallization peak could potentially be observed. However, it was not the case. This means that the sample had the time to crystallize during cooling. [12]
Finally, a melting peak (Tm) can be noticed slightly above 200 °C. This is a little bit lower than the value found in the literature : 217 °C. [5] This melting point means that the nylon is actually semicrystalline. Moreover, the area under the melting curve is linked to the degree of crystallinity (amount of crystalline material in the sample). [11] However, the shape of the melting peak does not look to be perfect, it could potentially be the combination of two different peaks. This can be explained by the presence of some impurities in the nylon which have a different metling point.
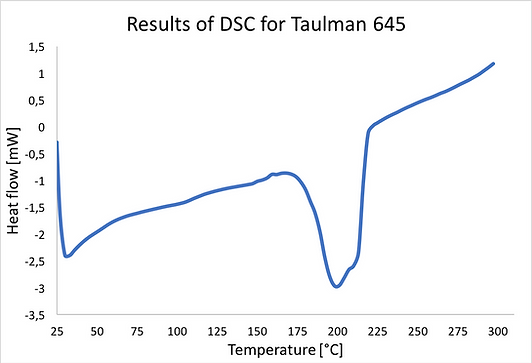
Figure 5 : Results of the DSC experiment for nylon Taulman 645.
>> Rheometry
Two rheometry experiments were performed on Taulman 645 samples. Notice that for these experiments, the samples were dried (60 °C during one night in a vacuum oven). The result of the first experiment at 220 °C can be observed on Figure 6. As the 3D printing can take some seconds, the angular frequency of interest is from 0,1 to 1 Hz. It can be deducted that the nylon has a quite viscous behaviour at this temperature but it is not in a newtonian flow state. Indeed, the curves of G’ and G" do not reach a slope of 2 for G’ and one of 1 for G". However, the sample often degrades before reaching this state. The experiment was then stopped at 250 °C because of the emergence of bubbles in the sample which would alter the results. Indeed, during the fusion of the three small samples, air was trapped in the nylon and bubbles appeared. This is why a second rheometry test was performed.

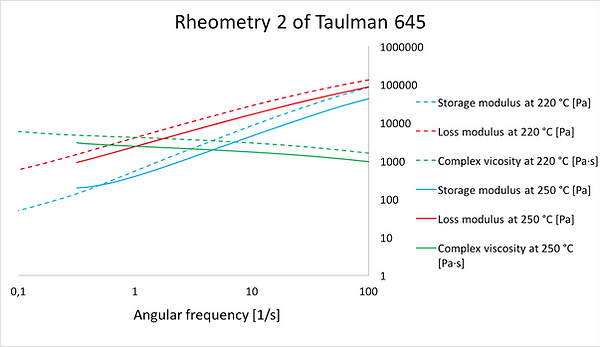
Figure 6 : Results of the first rheometry with Taulman 645 at 220°C.
The result of the second rheometry can be seen on Figure 7. For this experiment, two different temperatures were tested : 220 °C and 250 °C. Notice that the experiment was stopped before the end because of sample degradation. This degradation can be observed by an increase of the G’ curve (which was removed from the graph below). This is why the curve at 250 °C is not complete (data of the curve for frequencies lower than approximately 0.5 Hz are missing). It can be concluded that the nylon evolves quickly during the experiment and is not stable at 250 °C but it won’t cause any problem for 3D printing because the residence time at that temperature is much shorter for 3D printing than for the rheometry test.
​
It can also be noticed that we are in the terminal domain of relaxation because G" is higher than G’. The viscosity is quite constant which is normal because polyamide is supposed to melt at 220 °C. Therefore, a small shift of the temperature or the angular frequency will not induce a large modification of the viscosity. This makes it a quite robust material for the 3D printing process, as small changes in temperature will not cause a drastic behaviour difference of the polymer.
​
No huge difference between 220 °C and 250 °C can be noticed. This means that only a faster relaxation occurs when the sample is heated. This is the principle of time temperature superposition. Indeed, the temperature just shifts the relaxation time of the chains and so the velocity with which the sample relaxes.
​
The relaxation time is the time required to return to the base state of a polymer after being perturbated. [13] It can be obtained by the inverse of the frequency where G' and G" cross over in the flow transition regime. Thanks to Figure 7, it can be assumed that the cross over between G' and G" occurs approximately at a frequency of 200 Hz which means a relaxation time of 0.005 s.
​
The Cox-Merz rule states that "for many polymeric systems, correspondance occured between the steady-state shear viscosity in function of the shear rate and the complex viscosity in function of the frequency". [14] This means that the curve of the shear viscosity in function of the frequency and the one of the complex viscosity in function of the shear rate are similar as can be seen on Figure 8 (example for ABS polymer). Moreover, the cross over of these curves with the G' curve happens for the same frequency. So, a cross over between the complex viscosity and G' occurs at approximately 200 Hz too. After this shear rate, shear thinning appears, which is a decrease of the viscosity with the increasing shear rate. However, it only appears at a shear rate higher than 200 Hz which is really high and won't occur during 3D printing.
​
Figure 7 : results of the second rheometry with Taulman 645 at 220 °C and 250 °C.
> Conclusion
In conclusion, this polymer will be able to withstand temperatures higher than 180 °C. Moreover, it is durable, highly strong and shows good adhesion between the layers during printing. These properties could be attractive to build the mechanical parts of the drone. However, this polymer has some drawbacks too. Indeed, it has a hygroscopic behaviour which forces us to dry it before printing and compel us to not use water based solvent. Moreover, nylon is very difficult to use for dual-printing due to its high chemical resistance. This is why, Taulman 645 might not be the best suitable material for the 3D-printing of our drone.
> Bibliography
[1]”ORD Solution - 1lb Taulman 3D Printer filament 645 nylon”, http://www.ordsolutions.com/1lb-taulman-3d-printer-filament-645-nylon-1-75mm-clear/, accessed on 11/03/2017
[2] Zimmerman J., “Encyclopedia of polymer sciences and technology Vol11. : Polyamides”, Interscience publisher, New York, 1981.
[3] “The essential of chemical industry - polyamides”, http://www.essentialchemicalindustry.org/polymers/polyamides.html, accessed on 23/03/2017.
[4] “Polymerization of nylon 6“,http://nptel.ac.in/courses/116102010/3, accessed on 18/03/2017.
[5] “Taulman3D - Nylon 645 features”, http://taulman3d.com/nylon-645-spec.html, accessed on 16/03/2017.
[6] “Form futura - Taulman 645”, http://www.formfutura.com/285mm-nylon-filament-taulman-645-sale.html, accessed on 23/03/2017.
[7] “3D Prima - Taulman 645”, http://www.3dprima.com/en/filaments-for-3d-printers/nylon-175mm/taulman-645-nylon-175mm-filament.html, accessed on 11/03/2017.
[8]”Taulman3D - best print settings”, http://taulman3d.com/best-print-settings.html, accessed on 16/03/2017.
[9]”3D printing for beginners - What Material Should I Use For 3D Printing? – Advanced Materials Review #2 – Taulman 618 and Taulman 645 Nylon”, http://3dprintingforbeginners.com/3d-printing-materials-taulman-618-taulman-645/, accessed on 11/03/2017.
[10] "Airwolf 3D - Compatible dual material combinaitions",https://airwolf3d.com/3d-printing-tips/compatible-dual-material-combinations-3d-printing/ , accessed on 15/05/2017.
[11] Richard P. Chartoff and Anil K. Sircar, “Encyclopedia of polymer sciences and technology”, John Wiley & Sons, 2004, p11.
[12] John Scheirs, “Compositional and Failure Analysis of Polymers: A Practical Approach“, John Wiley & Sons, 2000, pp128-129.
[13] E.J. Hinch, "Lecture 1 : Introduction", https://www.whoi.edu/fileserver.do?id=28325&pt=10&p=17274, accessed on 07/05/2017.
[14] “The principle and applications of Cox-Merz rule”, TA Instruments, https://www.researchgate.net/file.PostFileLoader.html?id=55a6902c5dbbbdbb628b45dd&assetKey=AS%3A273813168689157%401442293555131, accessed on 30/04/2017.
[15] "Understanding the rheological characteristics of thermoplastic polymers", http://www.azom.com/article.aspx?ArticleID=12100, accessed on 07/05/2017.
​
Table 1 : Thermal properties.
Table 2 : Mechanical properties.
Table 3 : Printing features of Taulman 645.
Table 4 : Printing parameters for the dogbone.
Tm
+ Hâ‚‚O


EXO
ENDO
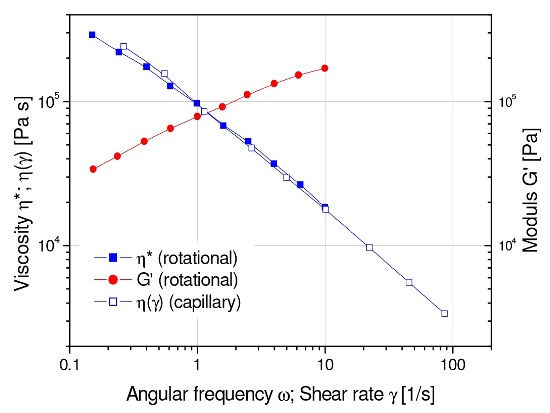
Figure 8 : Cox-Merz rule for ABS compound. [15]
By Julie
